REFLECTIVE GLASS
We have been continuing our activities for many years by prioritizing customer satisfaction.
REFLECTIVE GLASS
Reflective glass is essentially ordinary float glass with a metallic coating that cuts off solar heat. This special metallic coating also provides a one-way mirror effect, preventing visibility from the outside and thus preserving privacy. Reflective glass is used primarily for structural facade glazing.
Reflective Glass is Temka Glass’ reflective solar control glass.
The coated surface should be placed facing inside (surface no 2) of the Insulating Glass Unit.
High Reflective Glass is Temka Glass’ reflective solar control glass.
It can be used as monolithic and also it can be incorporated into Insulating Glass Unit with clear float glass or heat control coated glass.
REFLECTIVE GLASS
Reflective glass is essentially ordinary float glass with a metallic coating that cuts off solar heat. This special metallic coating also provides a one-way mirror effect, preventing visibility from the outside and thus preserving privacy. Reflective glass is used primarily for structural facade glazing.
Reflective Glass is Temka Glass’ reflective solar control glass.
The coated surface should be placed facing inside (surface no 2) of the Insulating Glass Unit.
High Reflective Glass is Temka Glass’ reflective solar control glass.
It can be used as monolithic and also it can be incorporated into Insulating Glass Unit with clear float glass or heat control coated glass.
Storage
Glass packs or crates should be stored at an angle of 5o from the vertical. If bowing of the crates is observed, they should not be stored further and the row should be unpacked immediately.
Glass packs or crates should not be stored outside. They should be stored in a closed environment where appropriate temperature and humidity conditions are provided. Recommended values for storage: temperature between 9-25oC, humidity <70%. During the storage of the packs and the crates, contact with rain, snow or any kind of water should be avoided. High risk of corrosion should be considered when the glass panes get wet during storage. Therefore, if the glass panes get wet because of condensation or any other reason, they should be cleaned immediately before drying.
The loading or unloading of the packs from the stillages should be well balanced.
For the storage of the Jumbo packs, wooden wedges with rubber are recommended.
For the storage of the machine or split sizes, wooden or metal (with rubber) wedges are recommended.
Stillage and the wedges should be supported with rubber pieces in order to tolerate the level differences that are originating from the ground.
Wooden wedges should be made out of hornbeam or beech that are dried in an oven.
Glass packs in which there are broken or cracked panes, must not be stored.
Care should be taken for minimum contact between the coated surface of Şişecam High Reflective Glass and the styrofoam. The styrofoam can leave spots that may be hardly removed on the coated surface.
Washing
Hardness of the water to be used for washing the glass panes should be maximum 5o Fr and pH should be between 6-8. The electrical conductivity of the washing water is recommended as 1 µS/cm for the glasses to be coated off-line and less than 30 µS/cm for insulating glass units. Brushes of the washing machine should be soft in order to avoid scratches on the glass. The water on the glass should be removed with air knife before drying.
Coated surface of Şişecam High Reflective Glass should not get into contact with the rollers. Friction to the rollers or other pieces should be avoided when the glass is conveying in the machine. Glass should be washed immediately after edge processing.
Carrying and Handling (in the plant)
During carrying/handling, cutting and edge processing; suction pads, conveyor belts, rollers or similar equipment should not get into contact with coated surface of Şişecam High Reflective Glass.
Glass packs or crates should be carried at an angle of 5o from the vertical. (Never horizontal) • Outdoor transportations should be made with closed vehicles that are protected from dust and water.
There should not be any broken or cracked panes inside the glass packs. Broken or cracked panes have the risk to scratch the glasses by side, and may cause injury.
Glass packs should be stepped on rubber or pad floor. Direct contact with metal or wood should be avoided.
An appropriate interleaving material such as powder or paper should be used between the glass panes. Inappropriate material can cause scratches, cracks and corrosion. In case of paper used as interleaving material, the pH should be between 5,5-7 and it should not leave any ash when it is burned.
All interleaving material should be clean and dry.
Loading and carrying equipment should be undamaged.
Glass packs or crates should be fastened to the vehicle during transportation.
Loading or unloading of the glass packs or crates to the vehicle should be carried out with appropriate equipment. Inappropriate equipment can cause accidents and breakages of glass. Removing the packages of glass should be made with care.
Cutting
During the cutting process, when supplying the cutting machine with glass, suction rubber should not get into contact with the coated surface of Şişecam High Reflective Glass. Touching the glass with bare hands should be avoided. Suitable clean gloves should be used.
Cutting wheel, cutting oil and cutting pressure should be used appropriate. A volatile cutting oil should be used.
The glass should be snapped off immediately after cutting process is completed.
The surfaces of the cutting tables should be clean and smooth.
The glass that will be cut should have the same temperature all around. Glass that is exposed to sunshine may not be cut properly because of the temporary stresses.
If glasses are heat-treated above 480oC, cutting and breaking problems can occur due to the secondary processes.
Processes
During the edge processing of Şişecam High Reflective Glass, applications that will cause pressure on the coated surface should be avoided. (Conveyor belts of the double sided grinding machines that are used for tightening the glass, the belts or handles of the drilling machines that are used for fixing the glass etc.) Before the tempering process, touching of the rollers to the coated surface should be avoided.
Şişecam High Reflective Glass should be seamed manually. If grinding process is necessary, then it should be carried with the machine that holds the glass from the uncoated surface. (like Intermac grinding machine for irregular shapes.) The liquids used should be tested whether they are appropriate to the coating.
Drilling is not recommended because of the pressure applied to the coated surface by glass holders.
Enameling
In order to ensure proper performances, enamel-coating compliance must be tested on case by case basis and the approval and warranties of enamel paint producers should be obtained. .
Tempering
Toughening should be done horizontally, avoiding rollers to get into contact with coated surface of Şişecam High Reflective Glass.
The temperature of the upper heating zones should be set minimum 20oC higher than the lower heating zones because the coated surface of the glass is upwards and will reflect the radiation coming from the resistances. Keeping the working rate of the ceramic rollers 10% lower than the working rate of the clear glass is recommended. • Tempering process will be carried easily with the forced convection tempering furnaces. The heating time will shorten and the distortions resulting from ceramic rollers will be less in the forced convection furnaces where the glasses are heated by using hot air.
After the tempering process, the spots may be seen more clearly, even if they wouldn’t be notified before the tempering process. Therefore care should be taken during the edge working process.
Insulating Glass Unit (IGU) Production
It is important to be sure that the glass cleaned well and the adhesion of the outer sealants to the coating is perfect. The sealant manufacturers’ guidelines should be followed and conformity tests should be carried.
During the IGU production, the aluminum intermediary spacer or any metal piece should not slide over the coated surface.
The coated surface should be faced inside the IGU (surface #2).
Cleaning
When glazed monolithically, the glass should be cleaned immediately after installation and as soon as it gets dirty. Mild detergents and gentle solvents should be used for cleaning. Sharp objects and abrasives should be avoided. After cleaning, the glasses should be rinsed thoroughly with clean water (preferably demineralized water).
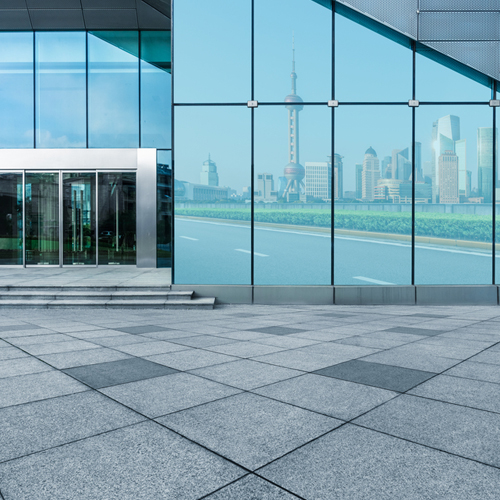
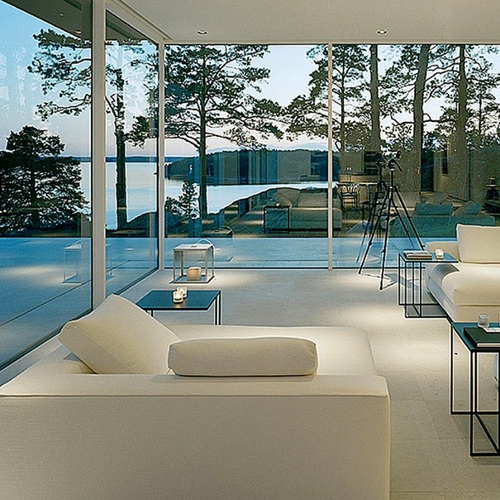
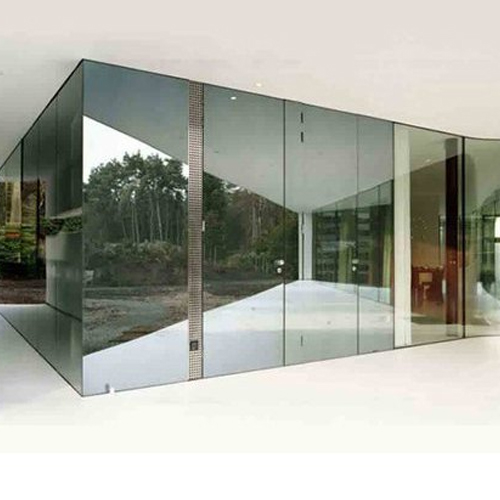