LAMINATION PROCESS
We have been continuing our activities for many years by prioritizing customer satisfaction.
LAMINATION PROCESS
It is process by combining two or more glass plates under the heat and pressure by means of Polyvinyl butyral (PVB) layer which is a special binding material.
Thermoplastic polyurethane (TPU) films can be joined using three different lamination methods, each providing distinct advantages depending on the application. Flame lamination employs an open flame to bond film to soft polyurethane foams, which are often subsequently processed by die-cutting. Adhesive lamination relies on hot-melt adhesives for smooth, flexible and temperature-resistant adhesion. Hot-melt lamination is ideal for bonding films with woven, non-woven, and knitted fabrics, as well as other substrates.
LAMINATION PROCESS
It is process by combining two or more glass plates under the heat and pressure by means of Polyvinyl butyral (PVB) layer which is a special binding material.
Thermoplastic polyurethane (TPU) films can be joined using three different lamination methods, each providing distinct advantages depending on the application. Flame lamination employs an open flame to bond film to soft polyurethane foams, which are often subsequently processed by die-cutting. Adhesive lamination relies on hot-melt adhesives for smooth, flexible and temperature-resistant adhesion. Hot-melt lamination is ideal for bonding films with woven, non-woven, and knitted fabrics, as well as other substrates.
Lamination Process Specifications
It minimizes the risks of glass breakage by keeping the parts in place in case of breakage.
It prevents ultraviolet rays by %97.
- Retains its overall integrity and continues to act as a barrier even if the glass breaks.
- Low-e coated laminated glass products reduce heat loss coefficient, keeping more heat inside the building.
Solar control and thermal insulation laminated glass helps saving energy by reducing cooling and heating expenses of the building.
Laminating Process
Laminating is the process through which two or more flexible packaging webs are joined together using a bonding agent. The substrates making up the webs may consist of films, papers, or aluminum foils. In general terms an adhesive is applied to the less absorbent substrate web, after which the second web is pressed against it to produce a duplex, or two-layer, laminate.
Applications
Web laminating is used to improve the appearance and barrier properties of substrates.
The choice of the most suitable web laminating process is mainly dictated by the end-use of the product. A number of different technologies are available that cover the wide variety of applications in the food and non-food packaging industries, as well as for the manufacture of technical laminates for the solar energy and insulation panel sectors.
Laminating machinery and laminating types
Laminating machinery can be classified according to the type of bonding agent used to produce the laminates. These types are:
Wet lamination: where the bonding agent is still in a liquid state when the webs are joined together. It is commonly used to produce a paper-aluminum foil laminate that is widely used in flexible packaging
Dry lamination: where the bonding agent, dissolved into a liquid (water or a solvent), is applied to one of the webs, before being evaporated in the drying oven. The adhesive coated web is laminated to the other under strong pressure and using heated rollers, which improves the bond strength of the laminate
Wax lamination: where the bonding agent is a wax or hot melt and is applied in a molten state onto one of the two substrates. This process allows the production of paper-paper or paper-aluminum foil laminates that are widely used for the packaging of biscuits and bakery products
Solventless lamination: where the adhesives used do not contain solvents. Solventless adhesive generally indicates a specific type of adhesive composed by two components reacting with each other and consequently not requiring drying.
The resulting laminated web is then rewound into a finished roll.
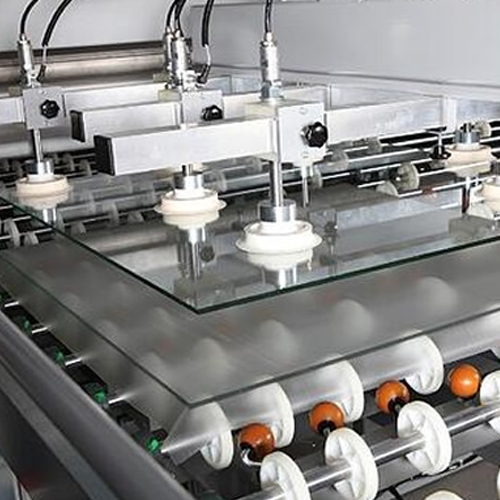
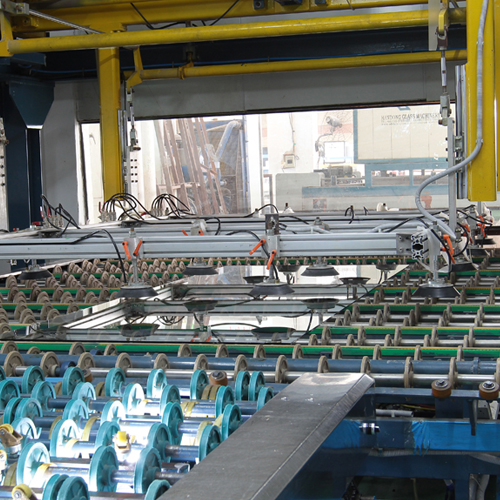
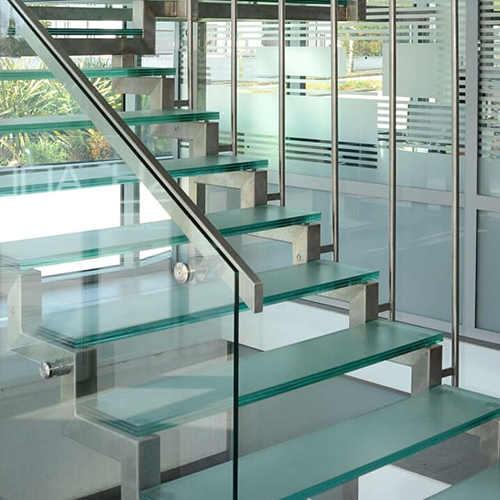